As the market for electric (EVs), hybrid electric (HEV) and plug in hybrid electric (PHEV) vehicles continues to grow, so does the need for the cooler, smaller lithium-ion battery packs that enable these automotive technologies. Because many lithium battery cells require joining a copper anode and aluminum cathode, the options for connecting the two dissimilar metals are limited, costly and can be unreliable in use.
Working with leading EV battery manufacturers, Materion developed a breakthrough solution with its copper-to-aluminum Dovetail Clad® metal. The material is produced by joining these two dissimilar metals side-by-side in long, continuous master coils.
Dovetail Clad material can easily be stamped and formed to create bus bars and lead tabs that can be conveniently fitted to lithium-ion battery packs. Bus bars and lead tabs made of Dovetail Clad metal are superior in mechanical, electrical and thermal performance over ultrasonic, bolted or mixed metal welded connections.
MATERION CLAD METAL PROCESS
Our cladding process achieves an excellent metallurgical bond by significantly reducing the cross-section and thermal diffusion to create a thin, ductile intermetallic compound. The result is a reliable copper-to-aluminum dovetail joint that matches the strength and fatigue toughness of the aluminum alloy.
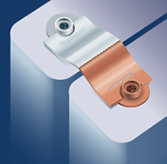
Dovetail Clad bus bars facilitate welding of like metals.
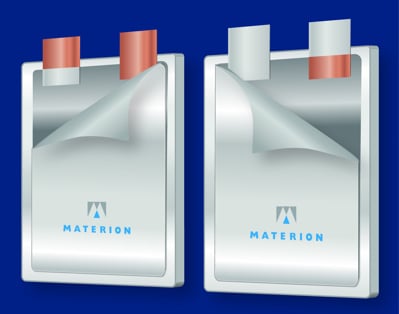
Replace anode or cathode with Dovetail Clad metal to simplify bussing.
DOVETAIL CLAD METAL DESIGN OPTIONS
• Aluminum Alloys: 1050, 1100, 1145
• Copper Alloys: C10200 with or without nickel or tin plating
• Thickness: 0.1 mm to 2.0 mm
• Width: Up to 115 mm
For partial penetration laser welding, we can provide a thick inlay solution that selectively clads a stripe of copper aluminum up to 50% of the metal substrate thickness. Download the thick inlay product brief for more information.
Benefits
- Lowest electrical resistance
- Smaller material dimensions & low height
- Easier welding of like material on bus bars
- Simplified bussing
Applications
- EV lead tabs
- EV bus bars